Metal Stamping Processes: From Prototyping to Mass Production
Metal Stamping Processes: From Prototyping to Mass Production
Blog Article
Enhancing Efficiency and Top Quality Through Modern Metal Stamping Approaches
As the needs for accuracy and performance proceed to rise, the combination of automation and digital tools right into the steel marking process has become paramount. By discovering the detailed interaction in between innovation, automation, and precision in steel marking, a pathway in the direction of unmatched performance and high quality assurance unfolds.
Advantages of Modern Metal Stamping
Modern steel marking offers numerous benefits in terms of efficiency, accuracy, and cost-effectiveness in the manufacturing industry. Among the crucial benefits of modern steel stamping is its ability to successfully create high volumes of intricate metal get rid of regular high quality. This process removes the requirement for multiple procedures as it can do different tasks such as blanking, puncturing, forming, and attracting in a single operation.
In addition, modern-day metal marking allows manufacturers to attain tight tolerances and exact specifications, ensuring that each part fulfills the needed standards. This high degree of precision results in minimal product waste, decreased rework, and overall better product quality.
Additionally, contemporary steel marking is a cost-effective manufacturing approach. In essence, modern metal stamping offers an affordable side to suppliers looking to boost productivity and quality in their operations.
Advanced Technologies in Metal Stamping

An additional crucial innovation revolutionizing steel stamping is the use of servo presses. Unlike typical mechanical presses, servo presses use higher control over the speed and force used during the marking procedure. This control not only boosts the high quality of the stamped components however also lowers material waste and power usage.
Furthermore, developments in simulation software have actually enabled suppliers to essentially evaluate and maximize the stamping procedure before physical manufacturing begins. This digital prototyping helps recognize prospective concerns early, leading to set you back savings and faster time-to-market for brand-new products. On the whole, these sophisticated modern technologies in steel stamping are driving extraordinary levels of performance and quality in the sector.
Improving Efficiency Via Automation
The integration of automated systems has actually considerably boosted the effectiveness of steel marking processes. Automation in steel stamping procedures provides a myriad of advantages, consisting of increased manufacturing rates, improved precision, and decreased labor expenses. By utilizing robotic arms and computer-controlled equipment, tasks that were previously taxing and susceptible to mistakes can currently be carried out swiftly and with exceptional precision.
Automated systems have the ability to handle repeated jobs with consistency, leading to greater performance levels and decreased cycle times. This raised performance not only causes set you back financial savings yet additionally makes certain a more structured and dependable production process. Additionally, automation allows for real-time tracking and data collection, enabling producers to determine and deal with problems explanation quickly, additional enhancing the general effectiveness of metal stamping operations.
Furthermore, automation promotes a safer working atmosphere by minimizing the need for hands-on intervention in hazardous tasks. By passing on these duties to automated systems, employees can concentrate on more facility and value-added tasks, contributing to a more reliable and effective process in the metal marking market.
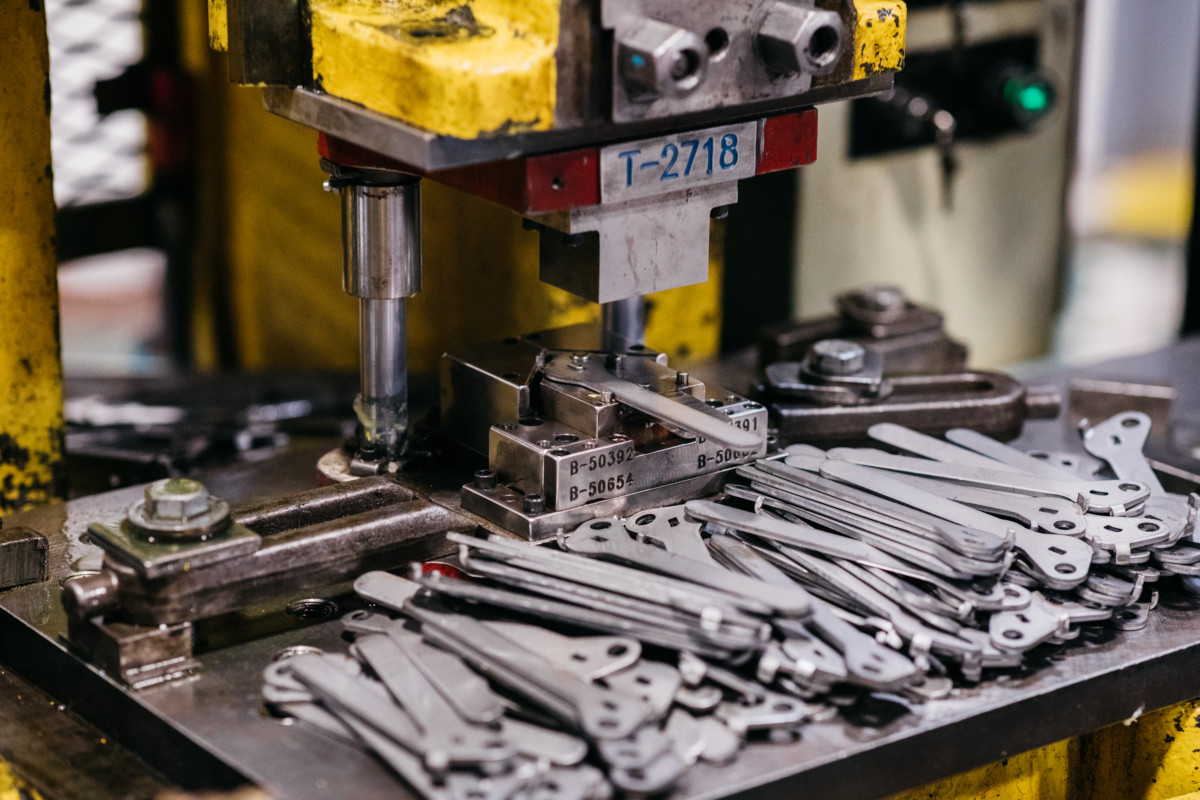
Quality Assurance Steps in Stamping
Implementing rigorous quality assurance measures is paramount in making certain the precision and uniformity of steel stamping procedures. By establishing robust top quality control procedures, manufacturers can recognize and correct any variances or problems in the stamped components, inevitably improving item high quality and customer contentment. Among the primary quality control procedures in metal marking is carrying out regular examinations throughout the manufacturing cycle. These evaluations entail inspecting the measurements, surface coating, and overall honesty of the stamped components to validate compliance with the specific demands.
Additionally, executing advanced innovations such as automated vision systems can even more enhance the top quality control procedure by enabling real-time monitoring and detection of any type of abnormalities throughout manufacturing. These systems utilize video cameras and computer algorithms to check components with high accuracy and precision, minimizing the risk of problems getting away right into the end product.
In addition, developing a detailed paperwork system that tapes high quality control data and evaluation results is essential for tracking efficiency fads and promoting continual renovation efforts. By examining this data, makers can determine prospective areas for optimization and implement rehabilitative activities to improve the general quality of their stamped items.
Enhancing Precision With Digital Devices
Utilizing digital devices can considerably enhance the accuracy of metal marking procedures, reinventing the way manufacturers attain accuracy in their manufacturing. Digital tools such as computer-aided design (CAD) software program enable the creation of detailed marking designs with exceptionally accurate dimensions. By inputting in-depth specifications right into the More Info software application, manufacturers can make certain that each stamped item satisfies specific dimensional demands, reducing mistakes and waste in the production procedure.
Additionally, the assimilation of sensors and real-time surveillance systems in stamping tools allows manufacturers to carefully monitor the stamping procedure and make instant adjustments to make sure specific results. These electronic tools click site supply important information on variables such as pressure, rate, and alignment, enabling for quick recognition and adjustment of any kind of variances from the preferred requirements.
Final Thought
Finally, modern-day metal stamping methods supply many advantages for enhancing efficiency and quality in making processes. By making use of sophisticated technologies, automation, quality control actions, and digital devices, business can boost efficiency, precision, and overall performance. These advancements in steel marking not just streamline production processes however likewise make certain consistent and top notch outcomes. Embracing these modern techniques can cause considerable innovations in the production industry.
Report this page